With the rise of Industry 4.0, robotization has become a big topic in the media space. "In manufacturing, though, robots are kind of taken for granted. They are a necessary condition for manufacturers to streamline production, reduce the amount of strenuous work and ensure the highest occupational safety possible. In our view, the main contribution of Industry 4.0 is in automation, digitization and working with data for timely decision-making and increased competitiveness," agree the Lát brothers, co-owners of the family company BENEŠ a LÁT. Josef Lát is the CSO and engineer, while Jan Lát is the CFO – as well as winner of the honourable title Manager of the Year Competition 2021 in the Czech Republic.
Robotization has allowed companies to save on manpower and associated costs. At the same time, however, energy costs went up, something that was not much addressed until the spring of 2021. Robots may not have human-like needs, but they are more energy-demanding both in operation and in stand-by mode. Given the higher costs, companies are starting to focus on eliminating non-productive energy.
Energy costs went up six times while production halved
"For about fifteen years, energy prices were roughly on the same level until the spring of 2021, when they started to increase fairly sharply. Foundry is one of the most energy-demanding industries. Until then, energy accounted for about 4%-5% of total costs. We would typically buy up to 20% of the expected consumption in advance, and although the forward prices may have been slightly higher than the spot ones, this was sort of an 'insurance policy' for us. The rest of the consumption was balanced on the spot market, as our consumption changes throughout the day and week, we could not secure more. But then there was the sudden change in the market behaviour.
While our monthly energy bills were around 70,000 to 80,000 EUR until March 2021, in August 2022 it was already 400,000 EUR. Being primary producers, our profitability is typically in the lower units of percent, so the steep increase in energy costs was significantly higher than our usual profitability rate. We monitor the main production parameters on a weekly basis and evaluate how many kilowatt hours it costs to produce each of our 1,600 products. So back in the summer of 2021 I had already drafted an energy clause for our customers, which factored in the energy consumption of each customer's portfolio. The model is open, and it copies the movement of energy prices on the energy exchange both up, and thankfully, also down over the last three quarters," explains Jan Lát, adding that back then, most customers had no idea what was going to happen in the coming months. "We don’t really want to increase prices at will to 'rip off' our clients. Our aim is to remain viable and maintain our supply chains."
The first person who advocated a wider use of data analytics and visualization both in production and R&D was Zdenko Piovarči, IT specialist who joined the company in 2003. Following his initiative, the company went on to build a central system to collect process data and logistics data as well as data from production facilities or from production line operators. This way, recurring issues are quick to spot and resolve in cooperation with other specialists. The data also feed algorithms which evaluate potential recurrence of failures, predict necessary maintenance and other issues that are otherwise hard to detect.
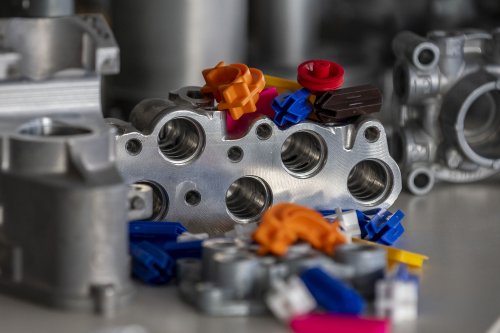
No industry can do without castings
Top-notch foundry work was practiced in the Czech lands already back in the Middle Ages. 20th century brought many innovations, with aluminium casting being particularly significant. Then, die casting technology was a ground-breaking discovery. For a modern industrial country, foundry is paramount, as evidenced by the 500+ foundries located in Czechoslovakia in 1918. And little has changed today, as most complex industrial products still cannot do without castings. Modern foundry technologies make it possible to produce parts with demanding shapes, which otherwise could not be produced at all, or only at a disproportionately high cost, if they their necessary properties were to be maintained.
BENEŠ a LÁT exports 80% of its production. Europe is the main export territory, with Hungary, Germany and Poland being the key markets. Lately, the demanding and metallurgically advanced Nordic markets with cheap energy sources have also shown some prospects. In the Nordics, the company delivers aluminium castings to manufacturers of ship drive units or even children's playgrounds. How did they succeed there, being a company from a resource-poor country with several times more expensive energy? (Note: As of mid-2021, a megawatt-hour of electricity for a Czech manufacturer cost about 40 to 50 EUR, while in Scandinavia it was 1.4 EUR.)
In the future, pretty much everyone will be a data analyst.
"They appreciated our proactive innovation and environment-friendly approach. Thanks to our R&D and cooperation with Cardam, we managed to comply with the technical parameters required by the customer and at the same time redesign (topologically optimize) the product so that its weight went down to 1.2 kg from the initial 2 kg. This resulted in reduced energy intensity of its production, material savings and lower transport costs, and thus a significant reduction in the carbon footprint," Josef Lát reveals. "The Nordics are also more open to their partners’ ideas and new, sustainable solutions – much more so than large European economies or multinational corporations."
Moving production closer to target markets is undoubtedly more feasible, given the lower production cost and the time saved in transport. According to McKinsey research, most manufacturers intend to relocate up to 20% of their production closer to their target markets by 2025. Many myths still prevail, though, like the dichotomy of industrial production vs environment, even where it’s not much expected. "Like many others, our Scandinavian partners believed that electrolysis from bauxite is the best way to produce aluminium. However, it is much more energy-intensive than obtaining aluminium by recycling from waste. In our industry, there is already so much of this raw material running around the planet that recycled aluminium is commonly used in companies like ours in their own production. Typically, only a few percent of new aluminium is added to it."
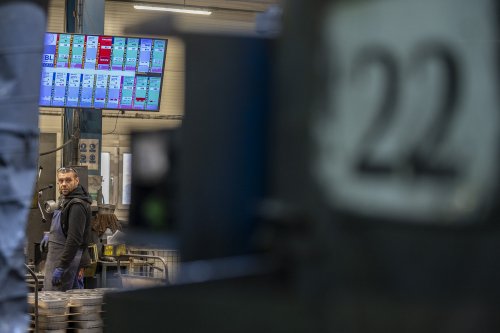
Diversification is proven crucial in every crisis
"Each crisis in our company’s modern history was different, and we also used different methods to tackle it. We’ve been lucky to have a fairly diversified manufacturing range since the early 2000s. We’ve defined a few simple rules. No customer should exceed a 15% share of total sales in the long term, and no market segment should account for more than 25% of our revenues. Today, 80% of our revenues is made up by as many as seven segments – mainly railway industry, forklifts, telecommunications equipment, automotive, hand tools and others. The other 20% is made up by food industry, medicine, children's toys and building blocks, and the like.
This wide range helped us cope with the 2008-9 crisis, as each segment went down at a different time. The years 2017-8 were demanding for us in a different way. All the segments grew at the same time, and the number of orders increased by dozens of percent compared to the previous period. On top, everyone wanted their order delivered ASAP. We started a four-shift operation, but some customers still had to wait for a while.
Then came covid measures, followed by semiconductor shortages, rising energy prices and the conflict in Ukraine. This time, however, compared to the past, the crisis has had impact on all segments. Multiple factors have come together and have been around for over three years in fact. None of the segments has shown any economic growth yet. On top, the rapid developments in the energy market have also brought about changes in the competitive environment. Moving forward, it will be more difficult to compete with foundry companies from the US and Southern Europe, where energy prices have grown a lot slower than here. Therefore, we see solid prospects in expanding our technology portfolio and further digitization and automation," conclude the family company representatives.
Written by Věra Vortelová
Photo credits: BENEŠ a LÁT